Brian is an entrepreneur and orthodontist with years of experience and a drive to grow his business. Constantly on the lookout for innovative approaches that will improve his practice and patients’ outcomes, he turned to Integrio to help him create a product that would empower independent providers to offer custom orthodontic devices.
Background
With the rapid advancements in 3D printing in recent years, the potential applications to dentistry and orthodontics have exploded. Using this technology, independent orthodontists can draw up prescriptions, print their own models, and manufacture aligners and other devices right in their own offices – an unprecedented degree of flexibility.
The challenge practices face in making the most of the opportunities present is managing the production and treatment process effective. For every patient, a provider must collect and store each patient’s information, track custom devices through a multistage production process, and monitor their use in treatment. When 3D printing first emerged as a driving force in the industry, many offices expected to make a few simple devices and manage their workflow with a whiteboard and perhaps a spreadsheet. Because of the large quantity of unique data required to create each patient’s device and treatment plan, however, it soon became clear that there was an urgent need for tools to structure and streamline production.
That’s why Brian decided to create a software product to help fellow orthodontists in the US and Canada manage every aspect of in-house, custom device manufacture and delivery. Armed with expert knowledge of the needs of orthodontic patients and providers, he partnered with Integrio to build the solution. The result of this collaboration is CAStrack, a multifunctional dashboard by orthodontists, for orthodontists.
Solution
Integrio has rich experience in developing production management software and database architecture for systems of any level of complexity. In this project, we focused on four key interfaces that we believe provide the greatest value to manufacture and treatment: a Special Dashboard, a Calendar View, a Detailed Patient Card, and a separate option for Tracking Multiple Office Workflows.
- The Dashboard can be filtered by office location and production track. It provides detailed views of all patients and their devices’ fabrication status.
- The Calendar View offers a bird’s eye view of device due dates and stage of manufacture, allowing offices to both closely monitor individual cases and quickly take the pulse of their workflow.
- Detailed Patient Cards allow providers to monitor and record treatment progress with custom devices. Besides, these individual records display up-to-date and detailed fabrication tracking, including which devices have been made, which software was used, and from what materials they were fabricated.
- Tracking Multiple Office Workflows helps orthodontists and their teams monitor and update production across multiple locations or practices. The customized functionality makes it possible to track and organize any digital workflow, including those of commercial labs.
Technologies
Results
Since Brian and his peers started using CAStrack, they’ve reported being able to provide care that is more personalized, in-depth, and efficient. Integrio carried out a detailed analysis of the impact CAStrack has had on users’ practices, and we found that these clinics have optimized their workflow and resource use, leading to both increased productivity and improved patient care.
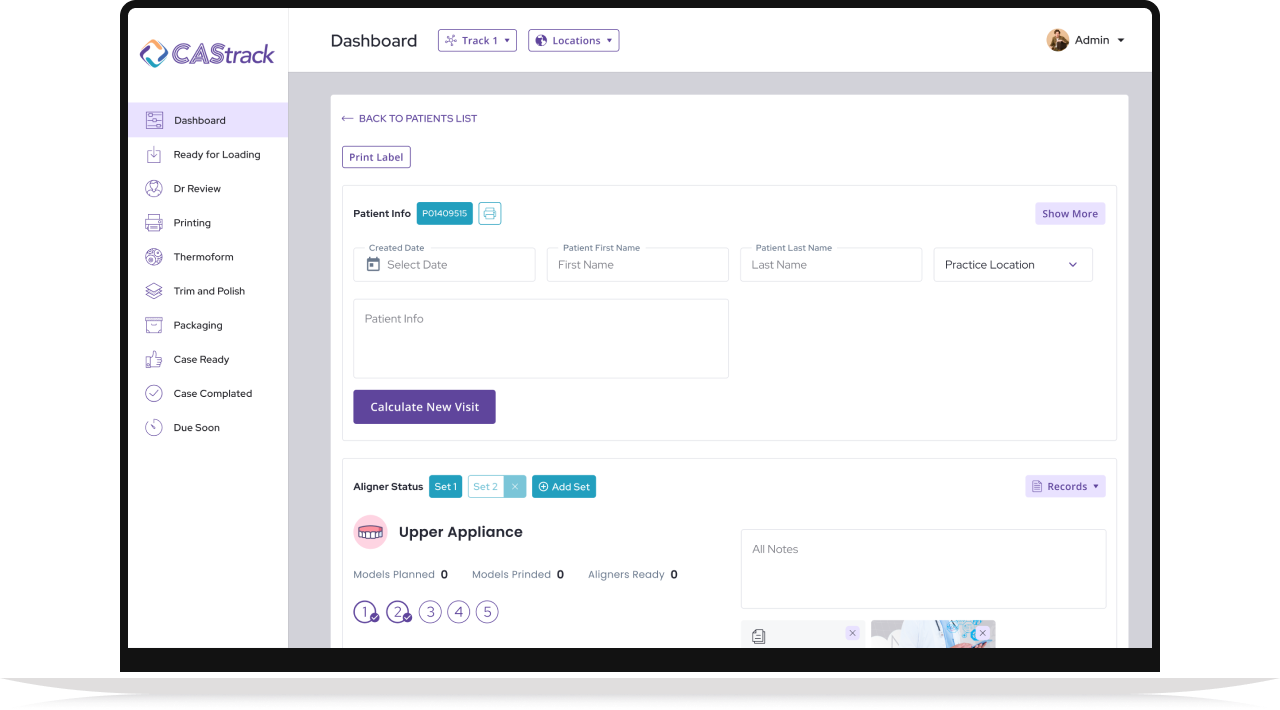
Case Studies
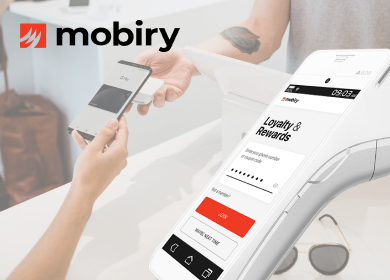
Mobiry
Mobiry is an AI-powered solution designed for brands active in omni-channel retail them boost sales and ROI.
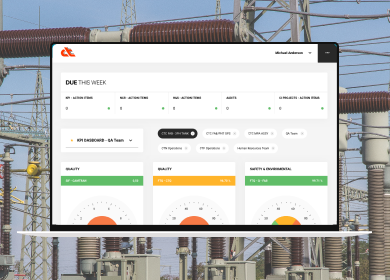
Cam Tran
Cam Tran is a Canadian company specializing in manufacturing, repair and renewal of all types of oil-filled distribution transformers.
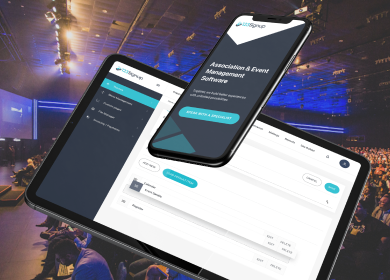
123Signup
123Signup is a market-leading SaaS solution for event & association management.
Contact us
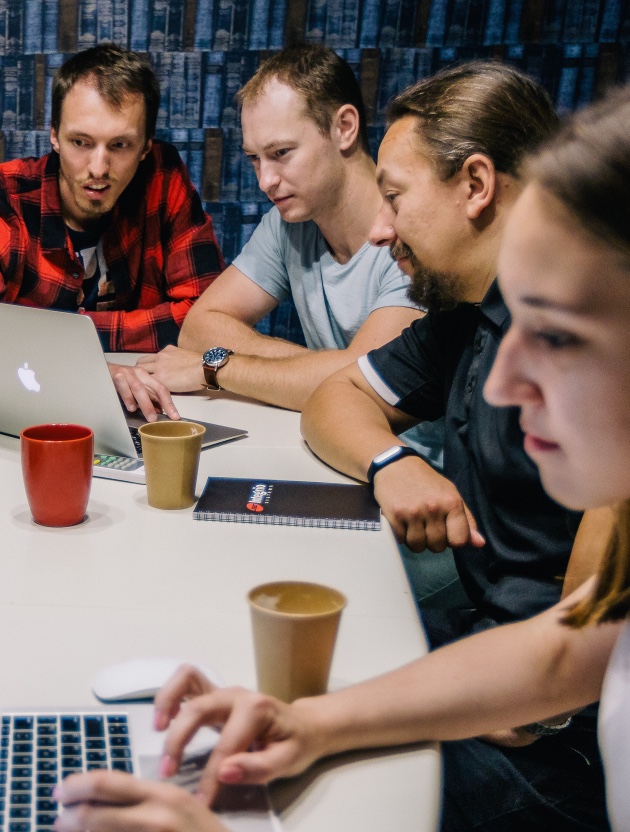