How Custom Manufacturing Software Powers Operational Excellence
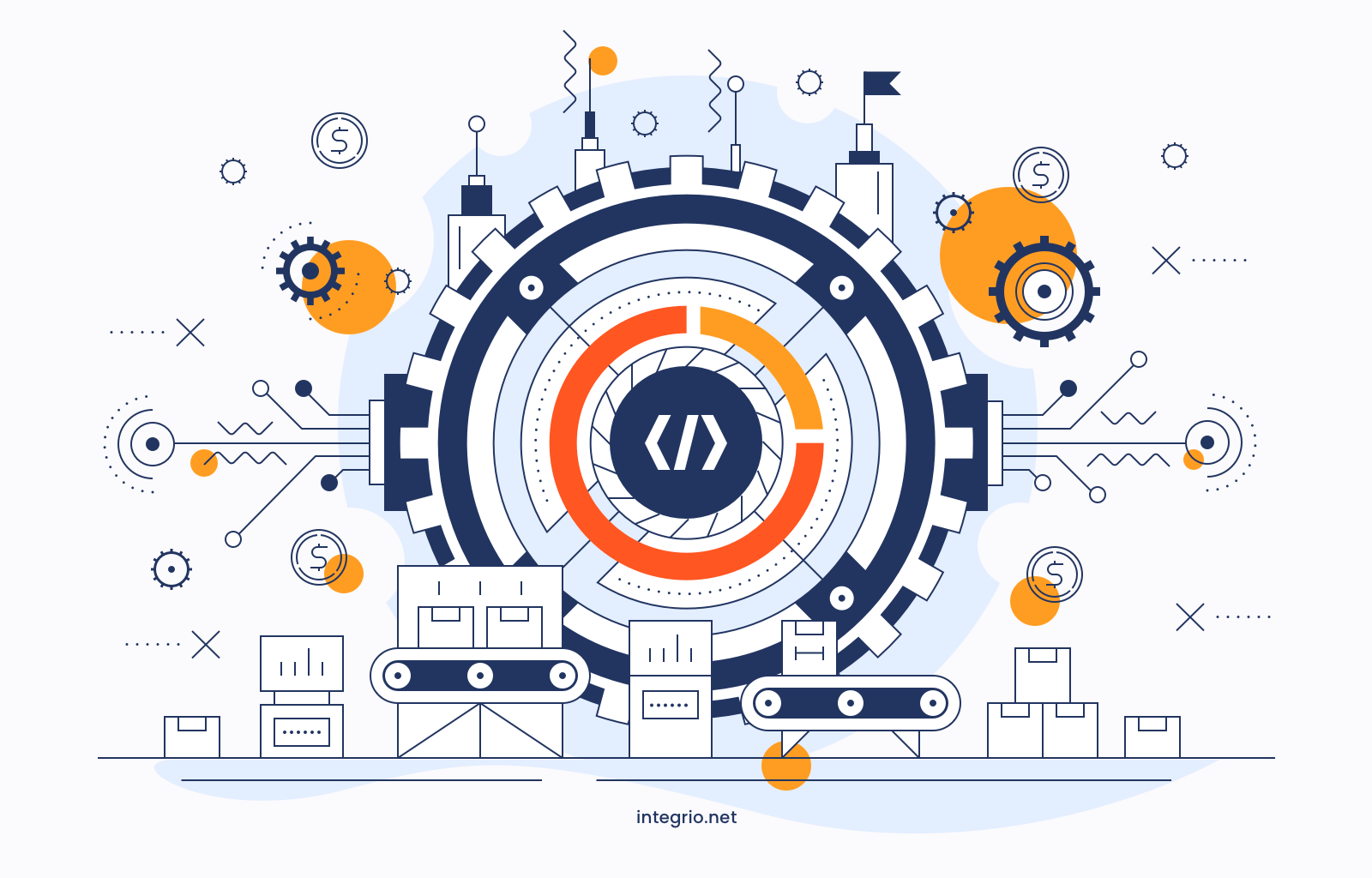
How much does unplanned downtime cost you? Your answer must be in hundreds of thousands of dollars per hour. The overwhelming majority of manufacturers (98%) report revenue losses of over $100,000 for every hour of downtime. A third estimates their losses to be in the ballpark of $1-5 million per hour.
These losses don’t have to be the cost of doing business, however. They are preventable, much like quality control bottlenecks and inventory shortages. All you need is the right custom software solution.
Here’s how custom manufacturing software systems can set you on a path to operational excellence by addressing the five common challenges.
5 Common Operational Challenges to Navigate
Custom manufacturing software solutions can address operational challenges like inefficient scheduling and resource allocation, unexpected downtime, and more.
Inefficient Scheduling and Resource Allocation
Unoptimized production schedules can cause industrial equipment to sit idle and skilled labor to work on low-priority tasks. Inefficient scheduling during peak periods can, in turn, cause employees to handle too many tasks, leading to fatigue and an increased risk of errors.
Shared resources, such as forklifts and vehicles, may also be double-booked or sit idle without proper tracking in manufacturing management software. An employee waiting for a forklift to become available is a perfect example of yet another bottleneck.
Equipment Downtime and Poor Maintenance Tracking
Unexpected equipment failure can effectively halt all activity on the shop floor, resulting in lost output and revenue. As a result, customers or distributors don’t get their products on time. Labor and other fixed costs continue accumulating. Emergency repair costs drive the losses even further.
This scenario usually unfolds due to a lack of full visibility into the equipment’s condition. Poor maintenance tracking can also cause some equipment to go without proper maintenance, potentially leading to unexpected downtime.
Inventory Visibility and Shortages
Lack of real-time inventory visibility may lead to unexpected shortages, which is a recipe for unplanned downtime and delayed deliveries. The inability to accurately predict demand (a feature common in some manufacturing software systems) can also lead to inventory shortages during peak periods.
On the other hand, outdated inventory information can lead to excess inventory. Unneeded inventory takes up valuable space, ties up capital, and may become obsolete or expire before being used.
Quality Control Bottlenecks
Quality control throughput that is lower than production volumes slows down the overall output rate. Reliance on manual workflows is the usual culprit in such scenarios. Those manual workflows typically include reporting on rejection reasons and requesting approvals.
Compliance Issues and Reporting Complexity
Manufacturers in heavily regulated industries, such as automotive, aerospace, and pharmaceuticals, must maintain detailed records of production processes and quality control results. Plus, all manufacturers have to comply with health and safety and due diligence regulations.
Non-compliance is a risky business: besides fines from the regulators, it can also tarnish the company’s reputation and lead to liability in civil courts.
Ensuring compliance without custom software, however, can mean hours of manual record-keeping, data entry, and report creation. Besides being time-consuming, manual workflows remain prone to human error.
How Custom Manufacturing Software Systems Address These Issues
Custom manufacturing software comes in many flavors, depending on its purpose. The most common types of manufacturing software include:
Enterprise resource planning (ERP) software
Computerized maintenance management systems (CMMS)
Computer-aided manufacturing (CAM)
Manufacturing execution system (MES)
Inventory management software
Environment, health, and safety (EHS) software
Preventive maintenance software
Manufacturing management software for the shop floor
Quality management systems (QMS)
Operations
Shop floor management tools can automate shift scheduling and task distribution for factory floor workers. Certain tools also include inventory management features with real-time tracking capabilities.
Manufacturing process management software can automate production planning based on stock availability, machine load, and available resources. This manufacturing operations software can also power production process optimization by reducing waste and rework, increasing uptime, and enabling process traceability.
Equipment Maintenance
Computerized maintenance management systems (CMMS) can help prevent unplanned downtime by tracking all completed and upcoming maintenance. As a single source of truth for equipment information, it can also streamline maintenance itself and prevent human error.
AI-powered predictive maintenance systems, in turn, can track a machine’s condition in real time using IoT data. Based on that data, those systems predict when maintenance is necessary.
Equipment Maintenance
Inventory, warehouse, and supply chain management features can be integrated into the ERP or shop floor management software. Alternatively, you can build a separate solution for these capabilities.
In either case, these features allow manufacturers to:
Track inventory levels and locations in real time across warehouses
Automatically match inventory to the production needs thanks to production pipeline integrations
Forecast demand and right-size inventory procurement accordingly with predictive analytics
Compliance
Any custom ERP for manufacturing usually includes risk management and compliance modules. They automate report generation based on real-time and historical data from the factory floor.
These features are tailored to the company’s context. For example, U.S.-based food and beverage manufacturers would be able to generate reports for the FDA based on the agency’s templates.
The EHS software, in turn, helps manufacturers track their safety-related measures, standardize practices, and monitor safety metrics. Automated report generation is also typically included in the EHS software.
Quality Assurance and Control
Dedicated quality management systems (QMS) help streamline the whole process, from approval routing and documentation to form and record management. Automating these processes reduces reliance on manual workflows, which speeds up quality control and mitigates the risk of human error.
A QMS also includes custom dashboards that visualize defect tolerances and rejection reasons. These provide comprehensive real-time data on product quality, allowing for more effective root-cause analysis.
4 Advantages of Custom Software Over Off-the-Shelf Solutions
Software for manufacturing companies can be either custom-built or purchased from software vendors. But unlike off-the-shelf solutions, custom industrial software development allows you to reap the following benefits:
Perfect workflow fit. A custom solution is built based on your unique workflows and industry-specific logic. Off-the-shelf tools, in turn, sometimes require adapting workflows to the tool’s capabilities instead.
Any integration possible. Certain equipment has a normal useful life of 15 to 40 years. If your equipment’s age is measured in decades, off-the-shelf tools are unlikely to support it. The same goes for legacy PLSs and barcode scanners.
User-specific UIs. Most vendor solutions have functionality-based interfaces, and the range of features can easily overwhelm an uninitiated user. Your custom solution can include a user-specific UI that displays only the features relevant to a specific role, making the learning curve a lot simpler.
Long-term agility and adaptability. Since you retain full ownership over a custom solution, you can easily adapt it to changes in production processes. This makes custom software a reliable asset in the long run. Off-the-shelf tools can’t be tweaked as easily.
Key Technologies Behind Custom Manufacturing Software
Manufacturing digital transformation is driven by cloud, generative AI, and 5G technologies: they deliver the highest ROI, according to Deloitte’s survey. Other high-ROI technologies include AI-powered data analytics and the Internet of Things (IoT).
Here’s how these and other technologies come together to power a custom manufacturing software solution.
Tech Stack
Any system consists of two major components: the interface and the underlying business logic. The interface can be built with a variety of tools, depending on the target platforms and devices, such as:
React
Angular
Flutter
The technologies for implementing the business logic also vary depending on the target platforms, as well as the required features. Common options include:
Node.js
Python
.NET
Integrations
Custom manufacturing software solutions have to be integrated with data sources, such as:
Industrial equipment
ERP systems
Custom MES (Manufacturing Execution System)
CRM systems
Factory automation software
Existing or custom-built APIs are the most common integration method. Other options include using middleware solutions or an event-driven architecture.
Deployment
Your custom software can be deployed either in the cloud or on-premises.
Cloud seems to be the preferred option for manufacturers, and 80% of them expect their cloud spending to continue increasing. Manufacturers typically opt for the cloud to replace or update existing systems or access new technology capabilities.
Cloud deployment is a must if your solution incorporates AI and ML features; they require cloud computing. It also tends to be more cost-efficient than on-premises deployment, as you don’t have to acquire and maintain servers yourself.
Data Analytics and Reporting
The collected raw data would be impossible to use as-is due to its sheer volume. Your system will need an analytics layer to power intuitive dashboards and visualizations and detect trends in the collected data. It also typically enables the automated generation of reports for specific use cases.
Optional: AI/ML and IoT
IoT sensors can collect data about the physical environment (e.g., temperature on the factory floor) and machinery condition and send it to the centralized software system. Alternatively, edge processing can be used to analyze it close to the data source.
AI/ML, in turn, power real-time predictive analytics used in predictive maintenance (based on IoT data), demand forecasting, and more. AI can also allow for simulating product line scenarios and processes to improve throughput and reduce costs.
Final Thoughts
Custom software for manufacturing companies does require a substantial upfront investment. That said, custom software will perfectly fit your unique workflows and use cases in a way that an off-the-shelf tool simply can’t. This makes it better positioned for resolving specific operational challenges — and addressing new issues as processes evolve in the long run.
Building such a solution, however, requires careful consideration of the underlying business processes, user expectations, available data, and analytics needs. You will also need expertise in data analytics, AI/ML, and IoT.
Integrio Systems has been developing custom manufacturing solutions that improve operations since 2000. Let’s discuss how we can help you reduce human error, eliminate bottlenecks, and improve efficiency with a custom solution.
Contact us
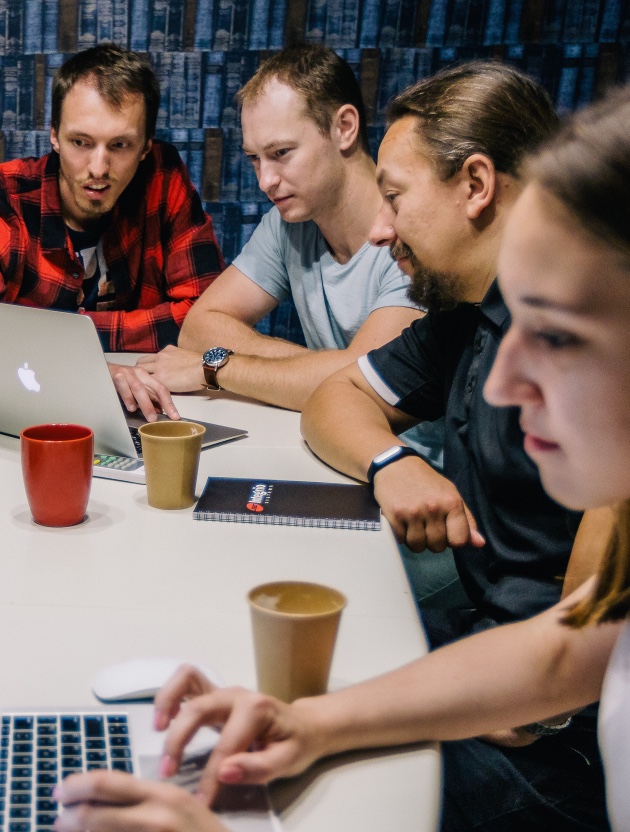